In this article
- Anomaly Detection in Industry
- The Importance of Anomaly Detection Across Various Industries
- Efficiency and Timing in Industrial Manufacturing: Reducing Costs and Gaining Competitive Advantage
- The Potential of AI for Anomaly Detection: Early Detection and Preventive Measures
- AI-Based Process Deviation Control – Increased Efficiency in Production
- Challenges and Solutions in Implementing AI-Based Anomaly Detection
- Increased Safety & Integration into Manufacturing Execution Systems
- Scalability, Precision & Data Protection
Anomaly Detection in Industry
Defective products that are improperly assembled or exhibit unexpected flaws are not only frustrating but can also have significant repercussions. Examples of manufacturing anomalies include a leaking flange, buttons that cannot be pushed, or products with inconsistencies in paint or altered surface textures.
Yet, what are the consequences of such anomalies? A mispositioned screw can render a product unusable, and faulty paintwork can lead to visual defects. Additionally, a change in humidity levels in the production hall can affect the material of the product, thereby reducing its safety standards.
The Importance of Anomaly Detection Across Various Industries
Deviations from expected production rates, product quality issues, or machine irregularities are classic examples of manufacturing anomalies such as sudden temperature fluctuations during the manufacturing process might indicate equipment malfunction.
In the energy sector, anomalies can signal issues with equipment performance, unusual consumption patterns, or potential power generation failures, such as spikes or drops in energy usage suggesting leaks or inefficiencies in distribution systems.
In financial services, unusual data patterns in transaction data might indicate potential fraud, money laundering or unexpected market movements. Detecting and analyzing these anomalies is a central issue for minimizing risks and ensuring efficiency and security in the various industries.
Challenges of Classic Anomaly Detection
- Rule-based approaches struggle to keep up with the increasing complexity of systems and growing data volumes, making them hard to scale.
- Manually setting rules is time-consuming and prone to errors.
- Analyzing high-dimensional and dynamic data is extremely complex.
- Static methods often fail to adapt to changing environments, leading to high false alarm rates.
- Frequent false alarms cause operators to ignore system alerts, highlighting the need for close collaboration with experts to develop effective systems.
Efficiency and Timing in Industrial Manufacturing: Reducing Costs and Gaining Competitive Advantage
In the era of globalization, efficient process planning is a competitive advantage in industrial manufacturing. Even brief production disruptions or logistics delays can slow down downstream process steps and production cycles, increasing operating costs. In industries such as semiconductor manufacturing, defect-related losses account for approximately 20-30% of production costs.
Additionally, operational disruptions result in: reduced inventory levels; supply shortages; longer delivery times, negatively impacting the entire supply chain.
While delays in delivery can lead to: expensive penalty fees; decreased customer satisfaction. Ultimately, anomalies can cause production to come to a halt.
The Potential of AI for Anomaly Detection: Early Detection and Preventive Measures
AI-driven approaches offer efficient solutions. Through machine learning and advanced algorithms, AI can provide scalable anomaly detection systems that automatically adapt to new data patterns. With machine learning you reduce the need for manual intervention and its costs, as well as lower the number of false alarms.
Thus, AI enables more precise and dynamic anomaly detection that meets the demands of modern businesses.
AI-Based Process Deviation Control – Increased Efficiency in Production
The proactive detection of anomalies using AI can minimize the reject rate and significantly reduce downtime in production. This results in higher utilization of manufacturing facilities and reduced supply bottlenecks. The result of automated anomaly detection: less downtime in production, direct cost savings, and higher profitability.
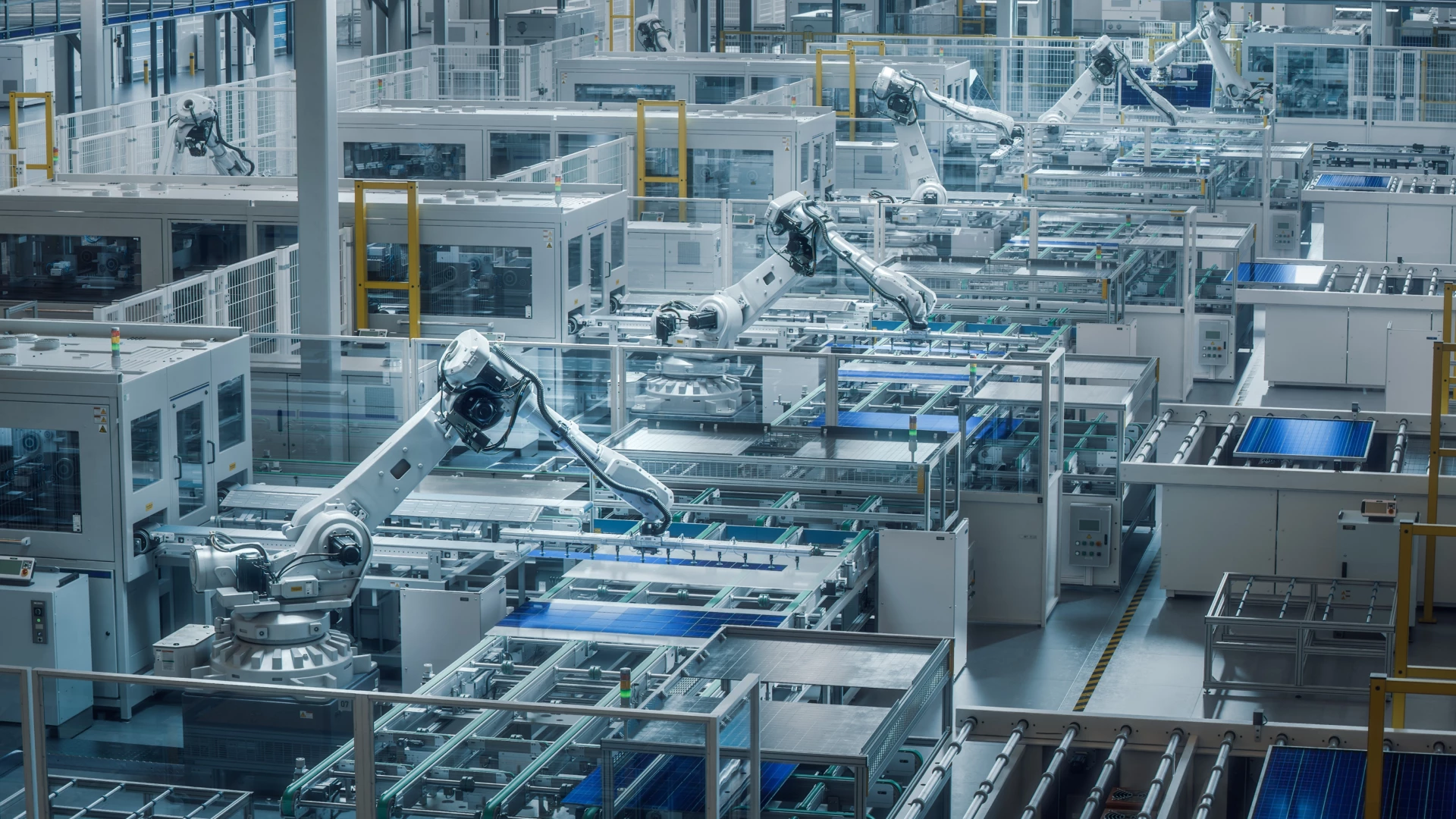
Challenges and Solutions in Implementing AI-Based Anomaly Detection
One of the biggest challenges in implementing AI-based anomaly detection is ensuring smooth integration into existing systems. This requires compatibility with existing systems and various hardware and software configurations.
Successfully deploying AI in this environment requires comprehensive training for the personnel responsible for operation and maintenance, as they need to understand the technical aspects of the algorithms and how to interpret and implement the insights gained.
Increased Safety & Integration into Manufacturing Execution Systems
With the seamless integration of AI-based anomaly detection into existing Manufacturing Execution Systems (MES), companies can improve operational efficiency and reduce downtime up to 20%.
Additionally, AI-based anomaly detection and reduction positively impacts product safety (quality & durability) and safety in manufacturing operations (especially for chemical and oil industries), including occupational safety, worker protection, and environmental protection. The latter plays an increasingly important role in regulatory requirements to prevent workplace accidents and harmful environmental impacts.
Scalability, Precision & Data Protection
One of the biggest advantages of AI-based anomaly detection is its ability to scale with increasing data volume and diversity, which manual systems cannot achieve. By reducing human errors, you improve precision and save valuable time in the entire manufacturing process.
On top of this, AI-based anomaly detection ensures compliance with strict data protection standards and regulatory requirements. Data control remains fully within the customer's systems, guaranteeing secure and data-protection-compliant operations.